Thermal Imaging
Specialists
Our infrared thermal imaging inspections can detect hidden faults within your electrical and mechanical systems, alerting you to potential issues before they escalate into serious fires, failures, or costly repairs.
We deliver hassle-free thermographic inspections with expert analysis and detailed reporting
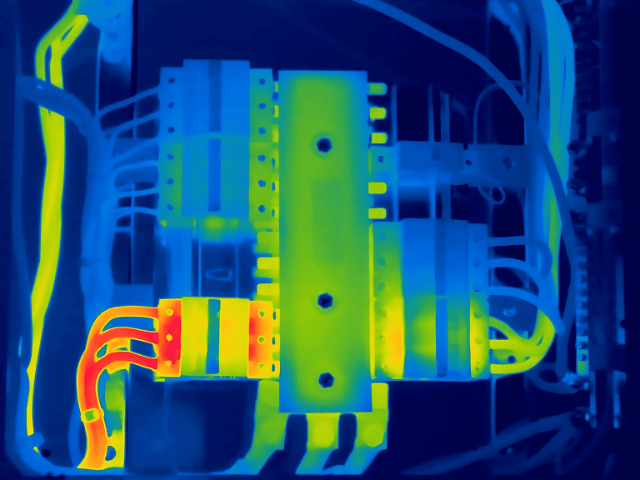
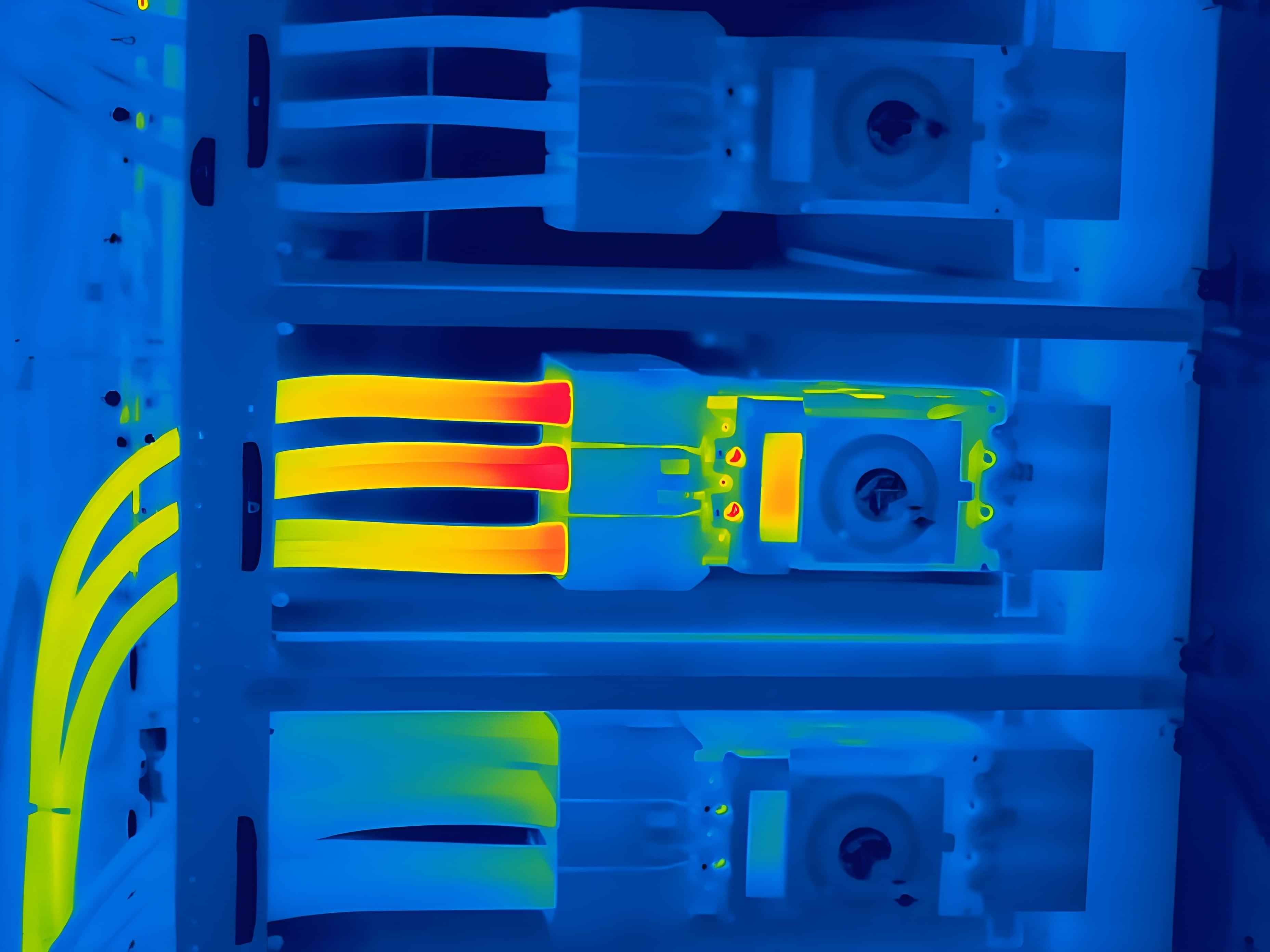
About Us
Based in Auckland, Galaxy Electrical specialises in providing cost-effective infrared thermal imaging services to a wide range of clients throughout New Zealand. From insurance compliance and preventative maintenance, to condition monitoring, construction validation, or simply peace of mind, we tailor our thermal imaging solutions to suit your requirements.
By utilising state-of-the-art FLIR thermal imaging cameras and software, our inspections can detect abnormal temperatures to help reduce the risk of fire, equipment failure, property damage, and downtime, while enhancing reliability, efficiency, and safety.
We are proud members of Quality Assured Master Electricians and have achieved SiteWise Gold Status for our health and safety systems. With ITC Certification, EWRB Registration, and extensive experience in electrical and mechanical systems, we deliver a reliable and professional service you can trust.
What Is Thermal Imaging?
Infrared thermography, also known as thermal imaging or thermographic inspection, is a non-destructive diagnostic technique used to acquire and analyse thermal information in real time. It allows us see temperature related issues that would otherwise be invisible to the naked eye.
An inspection is performed using a specialist thermal imaging camera that detects and measures the infrared radiation (heat) emitted from an object and converts it into a radiometric thermogram, otherwise known as a thermal image.
The thermal image displays different colours, each representing a specific temperature, to visualise heat patterns across the surface of an object. The image is then loaded into purpose-built software for detailed analysis and reporting.
Thermography is primarily used in electrical and mechanical applications to detect abnormal heat build up which could indicate a problem. Other common uses include building inspections, search and rescue, security, medical & veterinary applications.
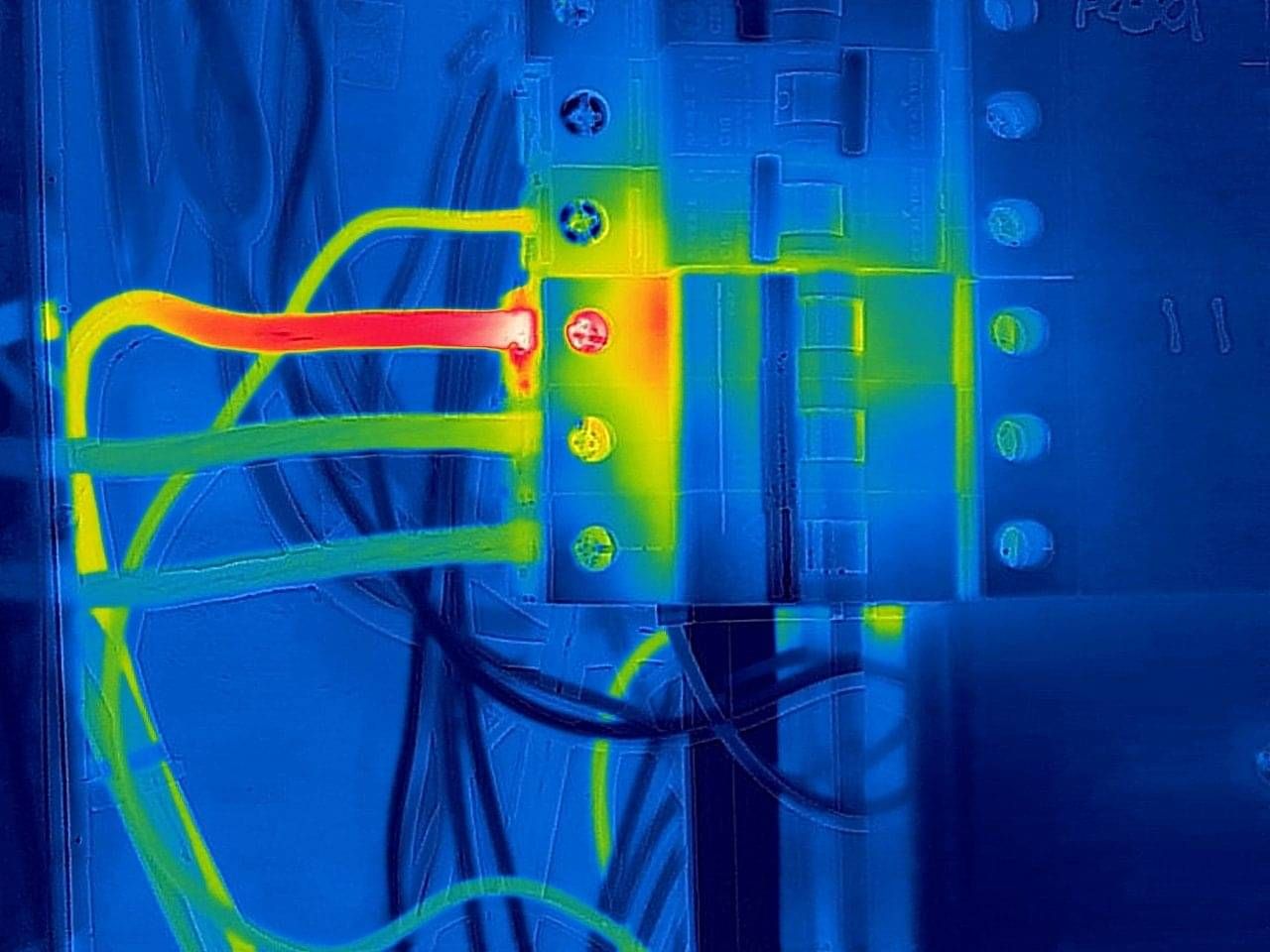

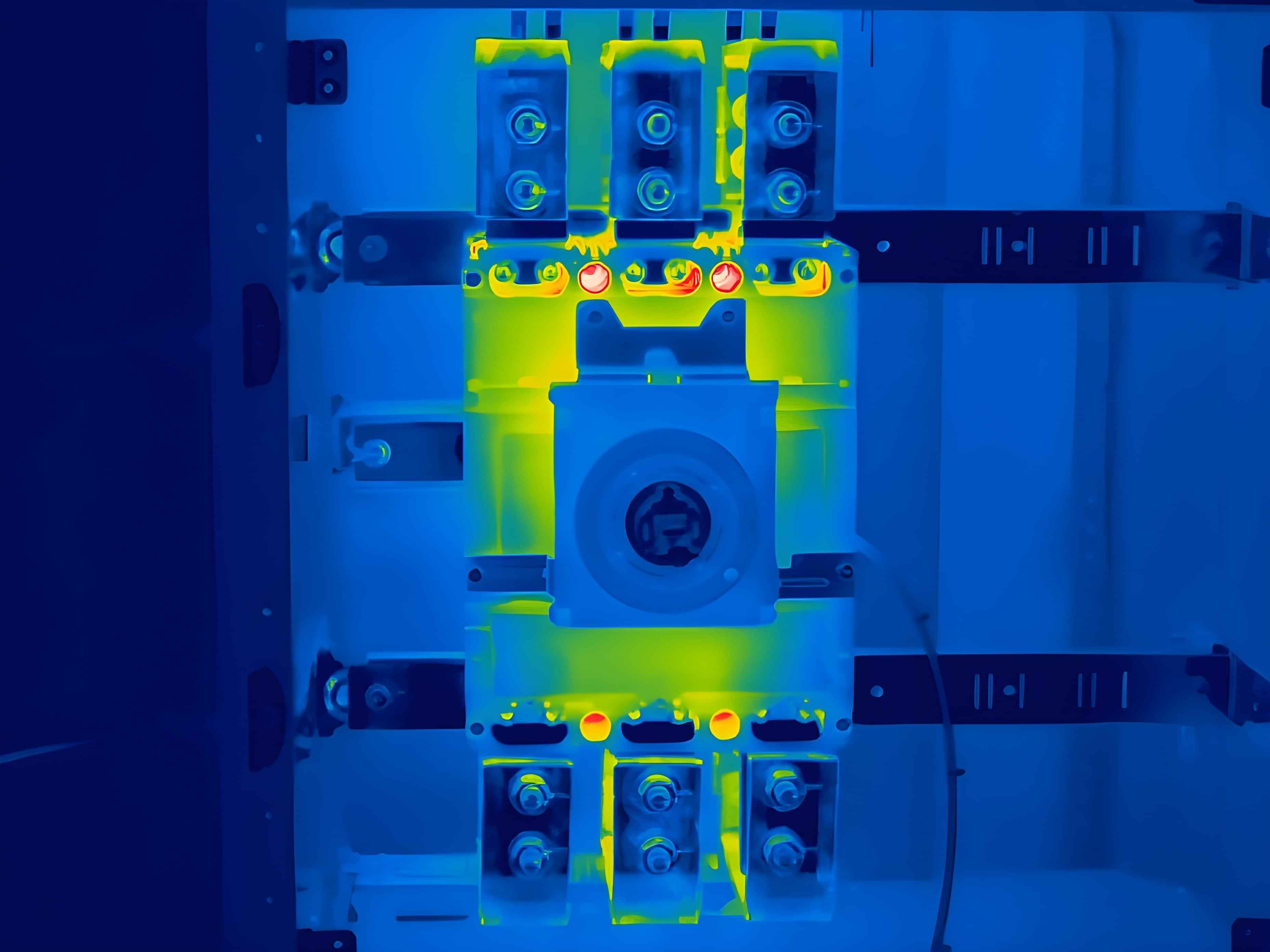
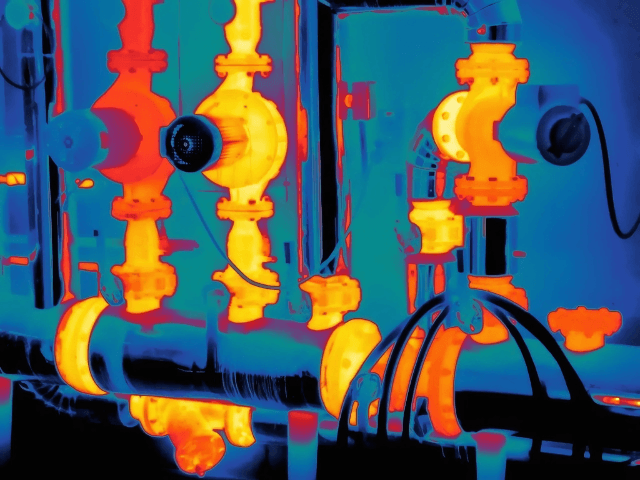
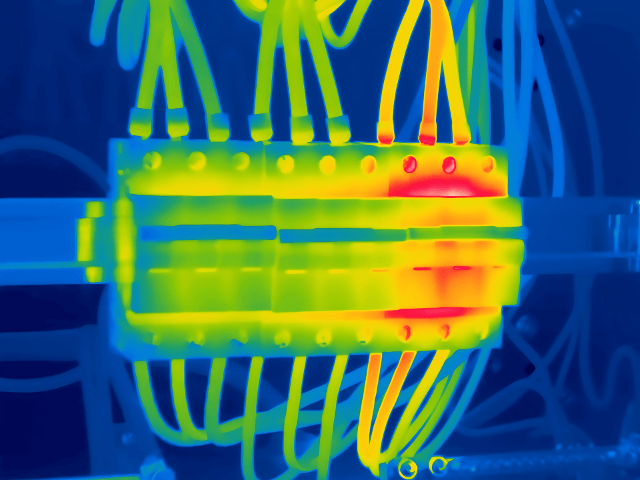
Why Do We Use Thermal Imaging?
Insurance Compliance
Insurance companies commonly require their clients to get an electrical thermal imaging report to help mitigate risk, prevent losses, and reduce claims and liability. Some insurers will even offer lower premiums if you get a regular inspection.
Preventative Maintenance
Find and address issues with precision before they become costly problems. It's much safer and cost effective to repair thermal faults before they escalate into events such as fire, equipment failure, property damage, and costly downtime.
Condition Monitoring
Production, processing, and manufacturing plants utilise regular thermal imaging inspections to monitor the condition of critical equipment for abnormal temperatures to enhance reliability, safety, cost efficiency, and to reduce downtime.
Construction Validation
Newly completed construction often requires a comprehensive thermal imaging inspection to satisfy the engineers and project managers that the installation is free from thermal defects, ready for handover to the client.
The Inspection Process
Step 1: We consult with you to determine the purpose, scope, and cost of the inspection. To ensure optimal results, we coordinate with you to schedule the inspection at a time when electrical and mechanical equipment is under load (operational). In most cases, our inspection will have no impact on your daily operations, allowing your business to continue as usual. For consistency and continuity, the same thermographer will always conduct your inspections.
Step 2: We evaluate the site conditions to identify potential access issues, risks, or hazards associated with the job, and prepare a detailed Job Safety Analysis (JSA). We will complete a site specific induction and permit to work if required.
Step 3: Our registered electrician/certified thermographer will safely carry out your inspection. Depending on the job, this may involve removing covers from electrical switchboards or guards from mechanical equipment to get a good view of the components. We exclusively use high resolution, calibrated, and accurate FLIR thermal imaging cameras.
Step 4: Once the inspection is complete, we ensure the site is left in a tidy and safe condition, and advise our site contact if we have found any faults or anomalies that require immediate attention.
Step 5: We load the images into our software for comprehensive analysis, and produce a clear and concise report containing thermal and visual images, object identification, fault classification, actionable recommendations, and all parameters relating to the inspection.

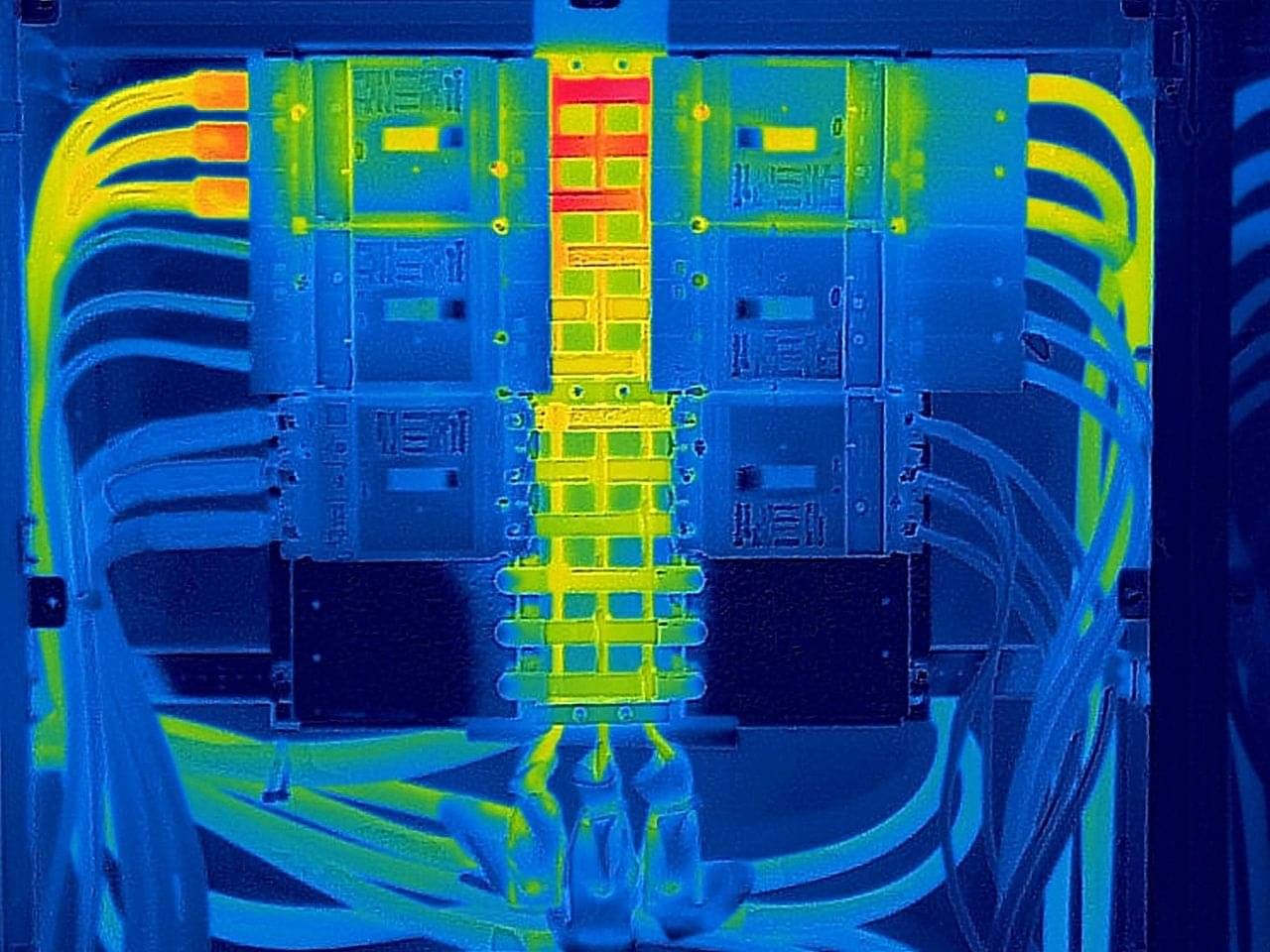
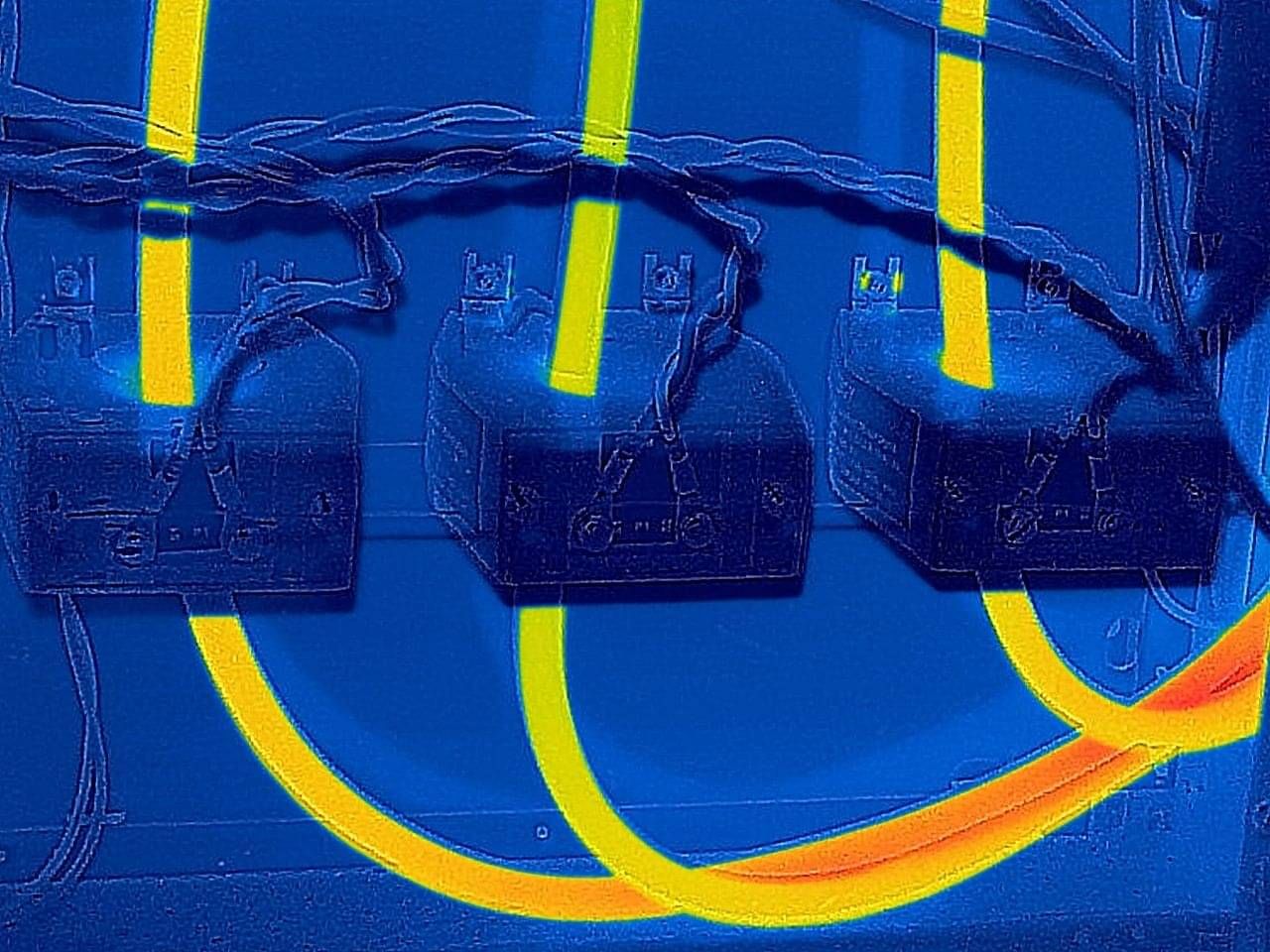